Investment Needed to Make Private Infrastructure Repairs
Private infrastructure repair must be as large of a priority as roads and bridges and that infrastructure includes boilers and furnaces.
By Rebecca Martin
As the tragedy and the scandal of Surfside keeps cascading like the storm surge of a hurricane, Americans are realizing that it is not just public infrastructure that is crumbling, but the very structures in which we live and breathe. See latest from NY Times. We grew up in a world that blindly believed that real estate investments were permanent, regardless of what we claimed on depreciation schedules for our tax returns might.
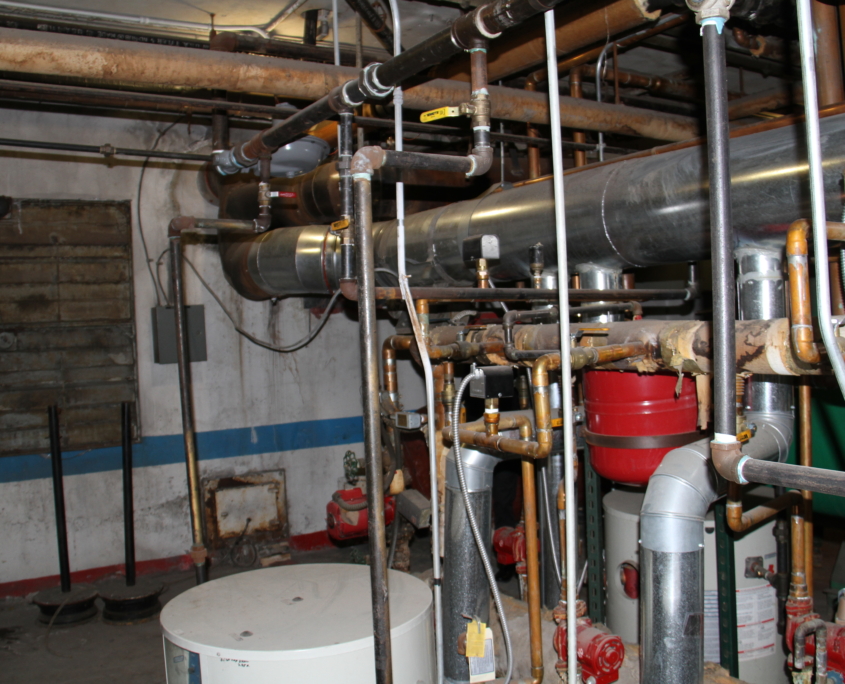
Keeping ourselves safe must include private infrastructure repair to aging boilers in hotels and commercial buildings.
But modern building techniques don’t rival wooden structures for longevity and it isn’t just the four walls of a building that can crumble, but the equipment inside of it. While the general public may be shocked to learn that most commercial buildings have little residual value at 40 years, those in the real estate, hotel and management business must know this. It is not just the high rises of the 1980’s that are at risk but all buildings where maintenance has been deferred and the concept of obsolescence forgotten.
While the cause of the Surfside catastrophe has yet to determined, intense scrutiny has turned upon those agencies responsible for decisions regarding construction standards and practices. Insurers were the first to react to the overall potential for danger in buildings 40 years old or older. Within days they were expressing their concerns, sending letters to owners of condominiums 40 years or older in South Florida. They requested proof that buildings have passed all inspections, giving owners a deadline for policy cancellation in 45 days if they were unable to comply or the option to simply cancel their policies. This is causing great concern to the South Florida housing market over decreasing insurance options.
This concern over the safety of older structures was exacerbated when another Florida condominium was found to be unsafe and evacuation orders were issued. The Crestview Towers is miles away from Champlain Towers, but using “an abundance of caution”, residents were forced to rapidly find alternate housing due to the fact that Crestview Towers had failed to get both its 40-year and 50-year recertification. It was found to be “structurally and electrically unsafe” according to the Washington Post’s July 2, 2021 article.
Florida’s regulations had already been updated following two earlier building collapses. In 1974, the federal Drug Enforcement Agency’s building collapsed due to an overloaded parking deck prompting a recertification program for older buildings. But these requirements were used in limited locations. In 1981, the Harbor Cay condominium collapsed during construction, which led to an overhaul of inspection requirements for buildings three stories and taller. It is expected that an investigation into the several agencies involved in construction, recertification and inspection will lead to new restrictions especially in coastal areas where sea water is also to be considered.
U.S. Infrastructure
The United States has been called to task over the state of our infrastructure for some time now. Infrastructure consists of many components. One such component is energy, which includes power plants and electric grids. We have looked in depth at what can happen when power grids fail or are not sufficient to the task. Other components include, drinking water systems, wastewater systems, broadband access, and buildings like schools. It also includes transportation such as roads, bridges, railways, subways, airports and harbors.
Now we are forced to look at another facet of US infrastructure and that is in the housing infrastructure. And similar to existing infrastructure issues, there is an underlying financial situation which will have to be addressed.
According to the Committee for Economic Development (CED), on addressing adequate road system for instance, we are not only looking at safety issues, there are substantial economic issues as well. Billions of hours are wasted by motorists dealing with traffic congestions, billions of gallons of fuel is wasted due to delays, and billions of dollars are spent on repairs and operating costs on vehicles annually. In addition, fatalities rise on deficient road systems.
Under the Trump Administration, the CED recommended that these types of deficiencies be addressed by the private sector in a sort of public/private partnership that not only addressed construction but usage as well. In this scenario, the financially privileged would pay to use uncontested lanes on highways to optimize time and money while others would be basically charged for usage. Our tax dollars at work for the upper class it seems.
This approach is worrisome to me when we turn our attention to the problems of structural integrity in older buildings which, in general, provide housing for those not in the upper financial tiers. The question arises as to who will absorb the inherent costs of insurance and repairs once the investigations have come to a conclusion?
But a bigger concern remains; will safety continue to take a backseat to financial concerns? Or will we continue to balance safety against costs going forward?
Private Infrastructure Repair: Commercial Boilers Need Replacement
We have looked at safety issues in older buildings in previous blogs. Whether it be refurbished hotels or schools, we have seen that improper installation and maintenance is often a serious issue. According to the U.S. Energy Information Administration, about half of all commercial buildings were constructed prior to 1980. And 46% of new commercial buildings are located in the south. Nearly half of all new construction since 2000 has been disproportionately located in the south. This breaks down to 29 years being the median age of buildings in the South compared to 46 years being the median in the Northeast. We can flip these numbers when speaking about the square footage with areas other than the South boasting larger square footage due to population demands. But the fact is that 72% of current U.S. buildings are more than 20 years old, and built with little concern for energy savings.
Operating costs have increased and the maintenance ‘to do’ lists continue to build in older properties. Yet these key components are not treated as private infrastructure must be. Too often the decision is to postpone replacement of HVAC equipment to get the most use out of outdated systems. According to a survey by Grainger, an industry distributor:
‘It’s no secret that costs are one of the biggest challenges of operating out of an aging building, but both time constraints and outdated systems also pose their own set of hurdles. “When we can’t get parts anymore or replacements don’t last or don’t work, then we move to upgrade,” one respondent points out.”
There are many objections to be made by owners of older commercial properties when making the decision to make private infrastructure boiler repairs. Obviously financial reasons are often cited. Then a belief that as long as the old system is working, it doesn’t need replacement. And a third consideration is the reality of a business shutdown for the duration of the installation. If the work is considered a repair, the cost and time involved in permits is avoided in many cases. And sometimes the decision to replace components rather than the entire system is made to avoid these circumstances. And too often the words “it was just inspected” seem a fragile defense in the event of a tragedy. And tragedies have occurred not only in the case of carbon monoxide poisonings but also in horrific boiler explosions usually involving inadequate maintenance and education on interlock safety.
According to an article on The National Board of Boiler and Pressure Vessel Inspectors by John R. Puskar, P.E.
“It seems we have hit a plateau with fuel and combustion equipment safety. Maybe it’s because of aging infrastructure or a lack of enforcement of existing codes and standards. Or it might be related to the economy – economic downturns often take a toll on safety, training, and maintenance dollars.“
He goes on to say that often inspections are farmed out to inspectors who do 90% of their work in the residential arena and who are fairly unfamiliar with commercial applications. And further, that 40% of all deaths and accidents are caused by human error or poor maintenance. As a result:
“The day after everyone has gone, and you’re now alone with your officially blessed equipment, one poorly trained person with a well-placed screwdriver can reduce your building to rubble and kill everyone around in less than five minutes.”
Much of the safety equation lies with a ongoing and consistent maintenance plan and proper ongoing documentation, even if the installation is entirely new. And this requires a certain amount of knowledge of the owners’ part when delegating those tasks to onsite maintenance or contractors.
An inspection is not always a guarantee that everything is fine. Code compliance is not retroactive and inspections usually rely on code compliance for the year the system was installed.
Commercial boilers have a lifespan between 15-30 years. Each year of operation will affect efficiency. And eventually, the ability to procure parts for repairs is impossible.
Older boilers are more prone to corrosion and the less new water that enters the system containing oxygen and minerals the better as these things combine to produce rust. Leaks develop further increasing the likelihood of corrosion. If corrosion exists in one place it is likely that corrosion exists throughout the system at an equal rate.
Another consideration with older heating systems is that those installed prior to 1972 likely involve asbestos. It was used at the pipe fittings and in some older cast iron boilers was present in asbestos rope used to seal in gases. This might not have been included in an inspection report.
In cases where the boiler is replaced, it is extremely important that how it meshes with the rest of the heating system is examined as it is always safest to assume that the original system was not installed properly and examine the entire system accordingly.
Hotel Private infrastructure Repairs in Hotels
One of the most concerning ramifications of considering the economics ahead of safety becomes clear when we look at lodging in the U.S. Sales of older facilities to new investors or owners have a very definite predisposition of what is important in refurbishing or renovating a lodging property for maximum impact. In almost every guide to successful hotel flipping available, the primary focus is on technology rather than powerhouse underneath. Whether it’s increasing bandwidth, providing up to date technology or streamlining hotel bookings… the economic focus is generally on technology and other surface improvements.
However, BPlans.com emphasizes that the first question that should be asked when purchasing a hotel is “Is the property up to code” and to familiarize oneself with local codes and regulations. And not to rely on the testimony of former owners on their level of diligence with maintaining the equipment and machinery. This all implies that as a commercial property owner, one has a certain level of responsibility in understanding the workings of the physical property and not delegating that entirely to others even if that is to the extent of being knowledgeable enough to ask the right questions of the maintenance crew before entrusting your venture to them. “It passed inspection” is no guarantee.
Residential Heating: Natural Draft Furnaces
Natural draft furnaces are older furnaces that use atmospheric pressure to push hot air out and cold air in to force out waste gases in the ventilation system. For more on the aging of natural draft furnaces, click here. These furnaces have an efficiency rating of between 65 and 70 percent. In 1987, the National Appliance Energy Conservation Act set a minimum efficiency for gas furnaces and water heaters at a minimum AFUE (Average Fuel Utilization Efficiency) of 78%. Today the minimum AFUE for a new furnace in the U.S. is 80%. This increased efficiency was accomplished by the addition of electric blowers to more efficiently distribute heat. All in all, fossil fuels are the primary fuel source for powering U.S homes. And much of the heat we use requires venting of some type which carries with it the risk of carbon monoxide.
It is interesting to note that the total use of energy in the U.S. has not changed much since the 1990s due to improvements in building materials and insulation, more efficient equipment and an overall population shift to areas which require less heating. Heating is a substantial use of energy in the U.S. the Northwest has the highest usage and also the oldest median age of homes; around 57 years of age. Older homes are more likely to have older systems. Recently the residential energy tax credit was reinstated and retroactive to 2018, encouraging homeowners to upgrade systems.
Newer furnaces offer greater efficiency but financial concerns have stalled efforts to raise efficiency requirements or encourage these non-venting systems. This is due to concerns over the fact that electricity is more expensive than fossil fuels and the increase in electrical use must be factored into the heating equation for homeowners. Your new furnace may require less fossil fuels but an increase in the use of electricity may raise heating costs substantially. At this point in time consumers will most likely opt out until a solution is found. The fact is that many homes in the U.S. still use natural draft furnaces which rely on atmospheric conditions for proper venting, although in some cases these have been retrofitted with newer parts to increase efficiency.
Leave a Reply
Want to join the discussion?Feel free to contribute!